HeatX Case Studies
HeatX is a disruptive technology designed to improve the efficiency and performance of power production, refining, and other industrial heat transfer industries
HECO Power Plant
Learn how HeatX significantly reduced biofouling and corrosion issues for Hawaiian Electric Company's (HECO) shell and tube heat exchangers at Kahe power plant
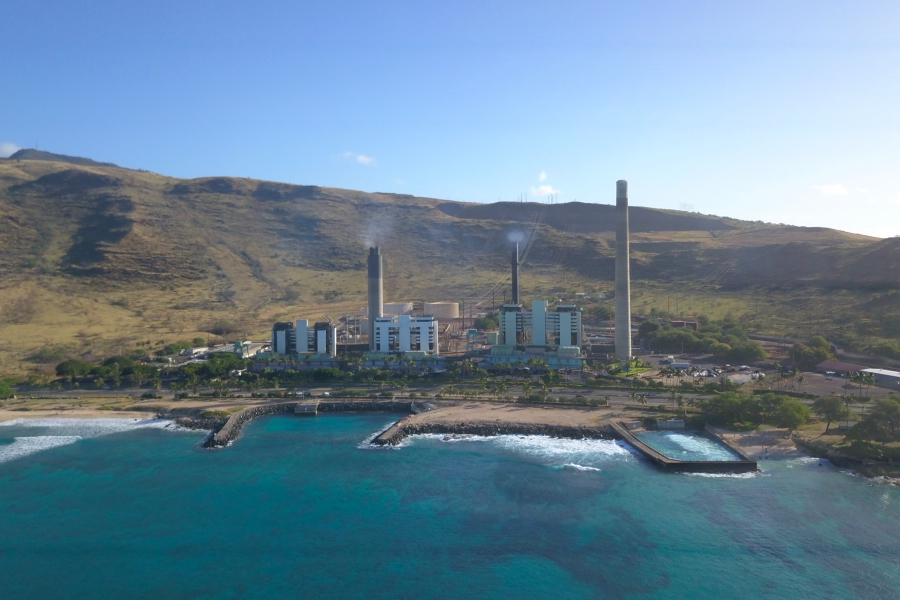

- Type of Facility: Thermal Power Plant
- Type of Heat Exchanger: Shell and Tube
- Material: Carbon Steel
- Number of Tubes: 1,000
- Year of Application: 2016
- Downtime Savings: 2 days/year
- 5-year Savings: $1.5 Million attributable to performance & efficiency gains
Middle East Desalination Plant
HeatX was applied to the 1200 MW Desalination Plant in the Middle East. Previously, the the heat exchanger experienced a high degree of corrosion and fouling due to the brine solution.
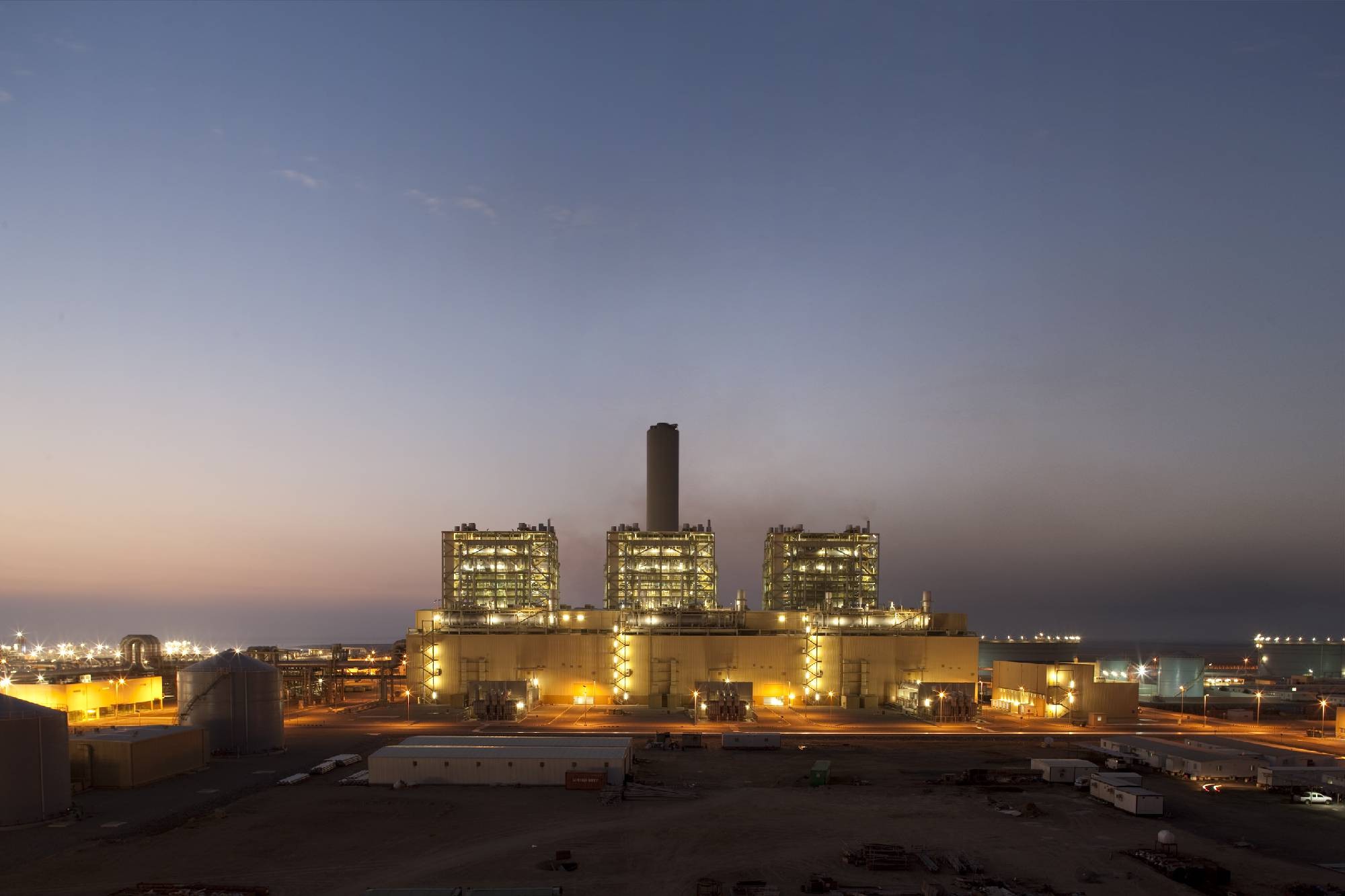

- Type of Facility: Desalination & Thermal Power Plant
- Type of Heat Exchanger: Shell and Tube
- Material: Copper Nickel Alloy
- Number of Tubes: 1,900
- Year of Application: 2018
- HeatX-treated unit delivered equivalent or better performance compared with titanium units
- Savings: $875K per year
Eni Arctic Refinery Production
HeatX was applied at an Eni S.p.A. production pad facility that was having numerous issues with shell and tube units used with process crude product coming from wells.
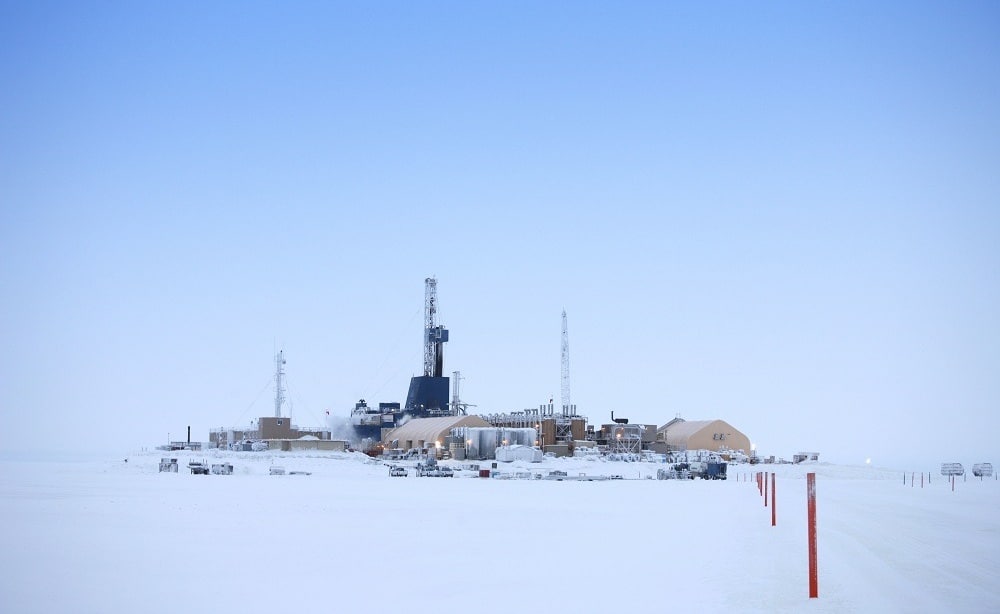
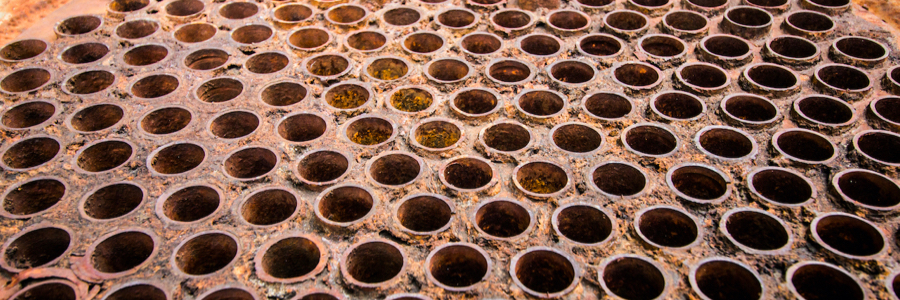
- Type of Facility: Upstream Production Pad
- Type of Heat Exchanger: Floating type Shell and Tube
- Material: Carbon Steel
- Number of Tubes: 1,600
- Year of Application: 2019
- Downtime Savings: Not a single shutdown for maintenance of the exchanger since HeatX application
- HeatX is now being adopted as gold standard for all facility HX units
O&G Refinery
Prior to HeatX, the heat exchanger had experienced massive amounts of deposition, erosion, and corrosion. Prior to HeatX, frequent acid cleaning was required which damaged the tubes.
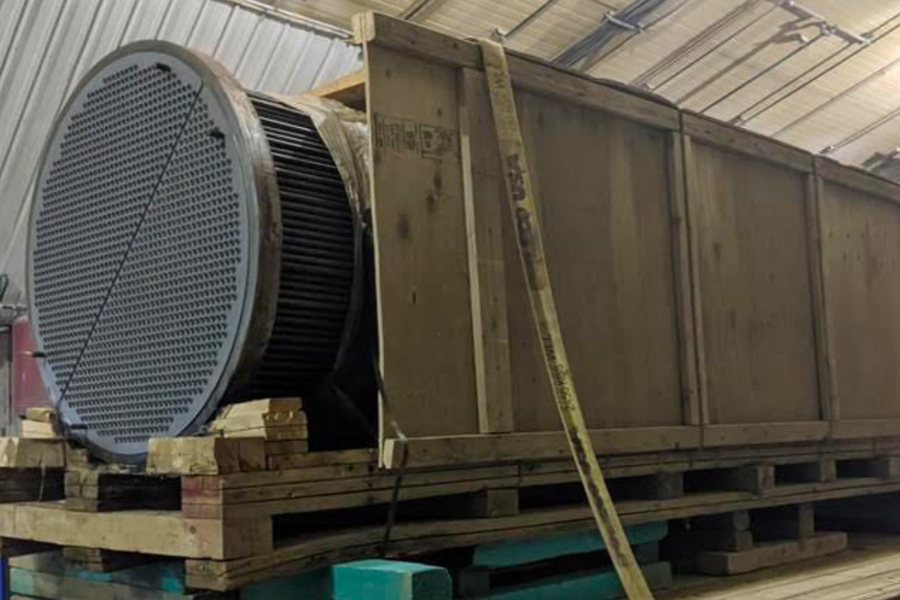
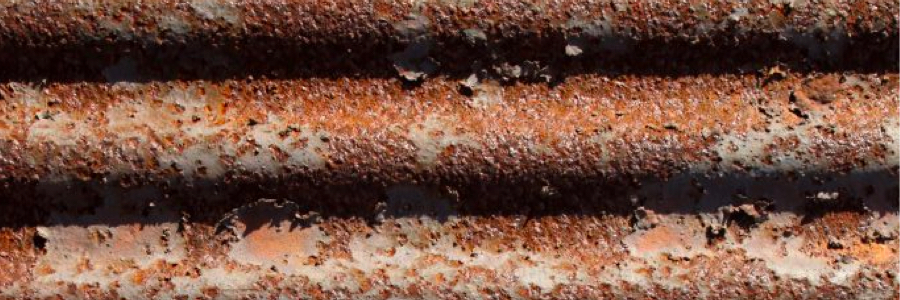
- Type of Facility: Desalination and Thermal Power Plant
- Type of Heat Exchanger: Floating type Shell and Tube
- Material: Carbon Steel
- Number of Tubes: 1,700
- Year of Application: 2017
- HeatX treated exchanger achieved equivalent efficiency as compared with a new exchanger
- Currently in service now with steady pressure, temperature and flow rate
Industrial Plant
HeatX was applied inside an industrial fertilizer plant during the shutdown period. Previous to HeatX, the heat exchanger experienced frequent shut downs due to tube blockage and lower heat transfer efficiency for service.


- Type of Facility: Fertilizer Plant
- Type of Heat Exchanger: Shell and Tube
- Material: Carbon Steel
- Number of Tubes: 2,900
- Year of Application: 2020
- Downtime Savings: Eliminated the need for plant shutdowns
- Improved flow and temperature conditions
- Life of the exchanger has been enhanced by more than 5 years